Understanding the Applications of Double Suction Pumps in Industry
Jul 21,2025
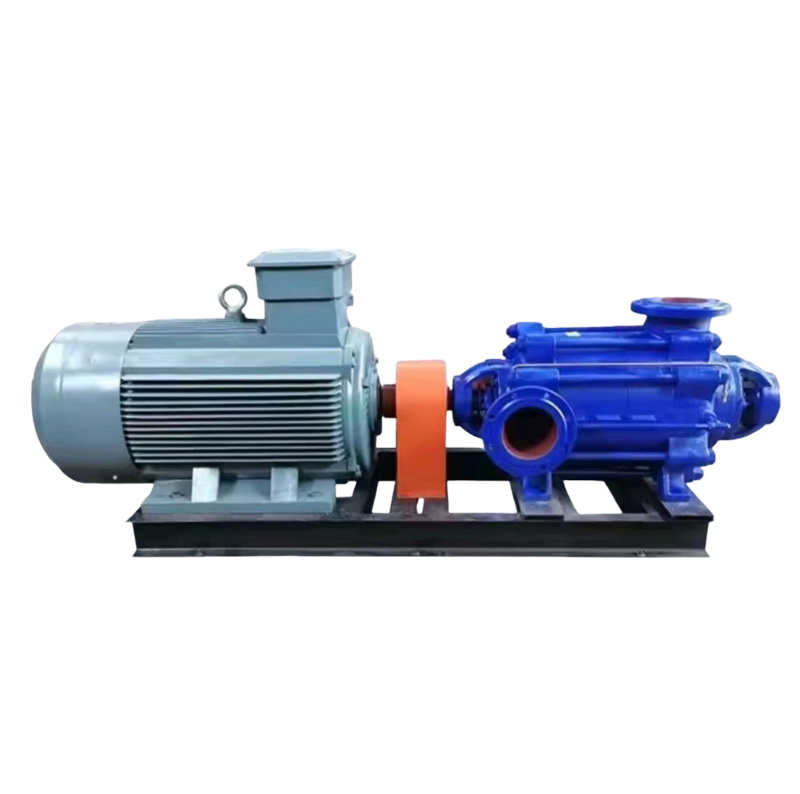
Understanding the Applications of Double Suction Pumps in Industry
Table of Contents
- Introduction to Double Suction Pumps
- How Double Suction Pumps Work
- Advantages of Double Suction Pumps
- Applications of Double Suction Pumps in Various Industries
- Maintenance of Double Suction Pumps
- Common Issues and Troubleshooting
- Future Trends in Double Suction Pump Technology
- Frequently Asked Questions
- Conclusion
Introduction to Double Suction Pumps
In the realm of industrial equipment, **double suction pumps** stand out due to their unique design and versatile applications. These centrifugal pumps are engineered to handle large volumes of fluids efficiently, making them indispensable in many sectors. With the capability to move liquids with minimal energy consumption, they have emerged as a preferred choice for industries requiring reliable and efficient fluid transport.
This article aims to provide an in-depth understanding of double suction pumps, focusing on their working principles, applications, advantages, and maintenance. By the end, you will appreciate their vital role in enhancing productivity across various industrial environments.
How Double Suction Pumps Work
Double suction pumps utilize a dual inlet configuration, allowing fluid to enter the impeller from both sides. This innovative design leads to several operational advantages. Let's break down the working mechanism:
Impeller Design
The impeller in a double suction pump is typically a **multi-blade** structure that efficiently converts mechanical energy into hydraulic energy. By drawing fluid from two sides, the impeller achieves a balance, minimizing axial thrust—resulting in less wear and tear on pump components.
Fluid Dynamics
As the impeller rotates, it creates a **centrifugal force** that propels the liquid outward, generating pressure. The fluid then exits through the pump's discharge nozzle. The dual inlet design not only increases flow rate but also enhances the pump's overall efficiency by reducing the likelihood of cavitation, a phenomenon that can damage pump components.
Advantages of Double Suction Pumps
Double suction pumps offer numerous advantages that make them an excellent choice for industrial applications:
High Efficiency
With their ability to handle large volumes of fluid effectively, double suction pumps demonstrate high operational efficiency. This efficiency translates into reduced energy costs, which is a significant consideration for large-scale operations.
Reduced Vibration and Noise
The symmetrical design of double suction pumps helps minimize vibrations and noise levels during operation. This characteristic is crucial for maintaining a safe and comfortable working environment.
Longer Lifespan
Reduced axial thrust and wear on components contribute to a longer lifespan for double suction pumps. This durability translates into lower maintenance costs and fewer disruptions in production.
Versatility
These pumps are highly versatile, capable of handling various fluids, including clean water, wastewater, chemicals, and slurries. This adaptability makes them suitable for a wide range of industrial sectors.
Applications of Double Suction Pumps in Various Industries
Double suction pumps find applications across various sectors due to their efficiency and reliability. Below are some critical industries where these pumps play a vital role:
Oil and Gas Industry
In the oil and gas sector, double suction pumps are essential for transporting crude oil and refined products. Their ability to handle viscous fluids and maintain high flow rates makes them ideal for drilling, production, and distribution processes. They are often employed in pipeline systems and offshore platforms, showcasing their robustness and reliability.
Water and Wastewater Management
Water treatment facilities and wastewater management systems benefit significantly from the use of double suction pumps. These pumps efficiently transport large volumes of water for treatment and distribution, playing a crucial role in ensuring clean and safe water supply. In wastewater applications, they manage the flow of sewage and industrial effluents, facilitating effective treatment processes.
Power Generation
In power generation plants, double suction pumps are utilized for cooling systems and circulating water. They ensure a consistent flow of water to maintain optimal operating temperatures, thereby enhancing the efficiency of turbines and other equipment. Their reliability in high-pressure environments makes them a staple in thermal and hydroelectric power generation.
Chemical Processing
The chemical processing industry relies on double suction pumps for transferring corrosive and viscous liquids. Their ability to handle varying fluid properties without compromising performance is crucial in maintaining safety and efficiency in manufacturing processes. From reactors to storage tanks, these pumps ensure a seamless flow of materials.
Maintenance of Double Suction Pumps
To ensure longevity and optimal performance, regular maintenance of double suction pumps is imperative. Here are some essential maintenance practices:
Routine Inspections
Conducting routine inspections helps identify potential issues before they escalate. Check for leaks, unusual vibrations, and noise levels during operation.
Lubrication
Proper lubrication of moving parts minimizes friction and wear. Regularly check and replace lubricants as per the manufacturer's recommendations.
Seal and Gasket Replacement
Wear and tear on seals and gaskets can lead to fluid leaks. Regularly inspect these components and replace them as necessary to maintain pump efficiency.
Performance Monitoring
Utilize performance monitoring tools to track flow rates, pressure levels, and energy consumption. This data can help identify inefficiencies and areas for improvement.
Common Issues and Troubleshooting
Despite their durability, double suction pumps may encounter issues over time. Here are some common problems and their troubleshooting methods:
Cavitation
Cavitation occurs when vapor bubbles form in the fluid and collapse, causing damage. To mitigate this, ensure the pump operates within its specified NPSH (Net Positive Suction Head) limits and check for any obstructions in the inlet.
Vibration Problems
Excessive vibrations may indicate misalignment or imbalance. Regularly check the alignment of the pump and motor, and ensure all components are securely fastened.
Leakage
Fluid leaks can arise from worn seals or gaskets. Inspect these components regularly and replace them as needed to maintain performance.
Future Trends in Double Suction Pump Technology
As industries evolve, so does the technology behind double suction pumps. Here are some emerging trends that are shaping the future of these essential devices:
Smart Pump Technology
With advancements in IoT (Internet of Things), smart double suction pumps are emerging. These pumps feature sensors and monitoring systems that provide real-time data on performance, enabling predictive maintenance and reducing downtime.
Energy Efficiency Standards
As industries strive to reduce their carbon footprint, the demand for energy-efficient pumps is growing. Manufacturers are focusing on designing pumps that consume less energy while maintaining high performance, aligning with global sustainability goals.
Advanced Materials
The development of advanced materials resistant to corrosion and wear is enhancing the durability of double suction pumps. These innovations lead to longer lifespans and reduced maintenance requirements, making them more cost-effective in the long run.
Frequently Asked Questions
1. What is a double suction pump?
A double suction pump is a type of centrifugal pump that draws fluid from two sides of the impeller, allowing for high flow rates and reduced axial thrust.
2. What are the primary applications of double suction pumps?
They are widely used in the oil and gas, water and wastewater management, power generation, and chemical processing industries.
3. How do I maintain a double suction pump?
Regular maintenance includes routine inspections, lubrication, seal and gasket replacements, and performance monitoring.
4. What are common issues with double suction pumps?
Common issues include cavitation, vibration problems, and leakage. Regular maintenance can help mitigate these problems.
5. What are the future trends in double suction pump technology?
Future trends include smart pump technology, increased energy efficiency, and the use of advanced materials for enhanced durability.
Conclusion
Double suction pumps are indispensable in various industrial applications, thanks to their efficiency, versatility, and reliability. Their unique design not only optimizes performance but also contributes to cost savings and sustainability in fluid handling processes. Understanding their applications and maintenance requirements is crucial for industries looking to enhance productivity and reduce operational risks. As technology continues to advance, embracing innovations in double suction pump design and functionality will pave the way for more efficient industrial operations in the future.
PREVIOUS:
Contact Us
E-mail :
liu@cnpumpmade.com
WhatsApp:
+8615028256698
Address:
Nanyang Industrial Park, Shifo Town, Anguo City, Hebei Province, China